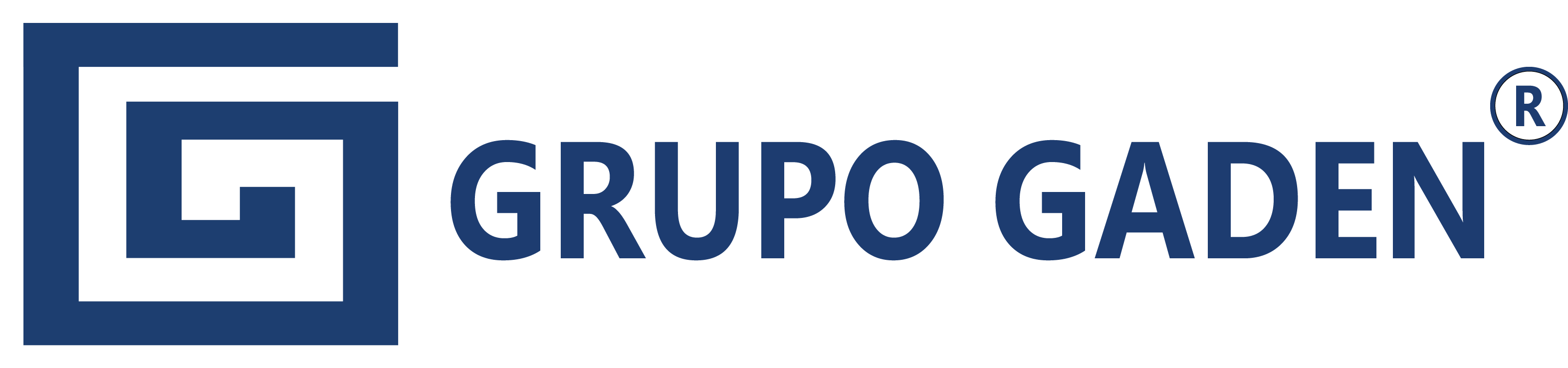
EXTRACTORES PARA CNC
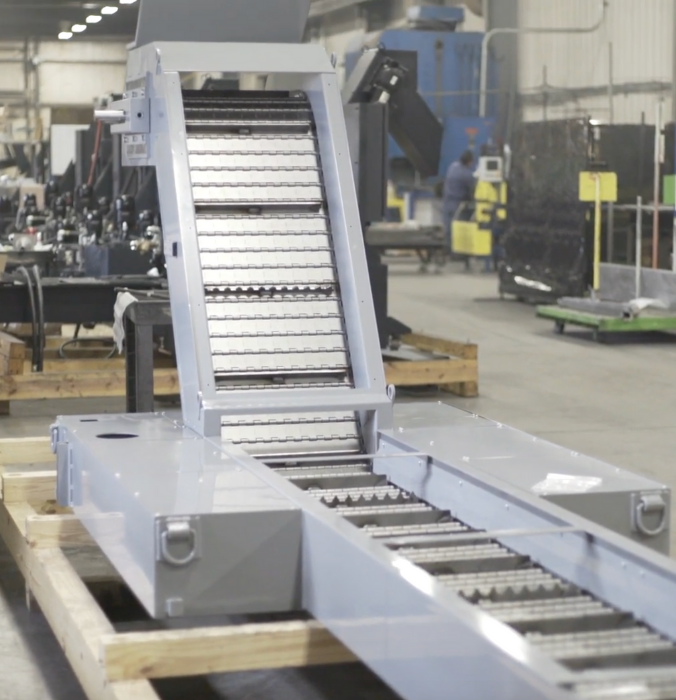
INCREMENTE LA PRODUCTIVIDAD
Automatice la eliminación de rebaba e incremente la productividad de mecanizado con soluciones que eliminan los desechos de sus procesos de forma segura.
Los sistemas se crean en función de sus requisitos y pueden personalizarse para gestionar cualquier tipo de rebaba y material, desecho, pieza, refrigerante y filtración de refrigerante.
Localice su centro de servicio GADEN más cercano y con gusto lo ayudaremos.

Productos
EXTRACTORES Y FILTRACIÓN
Nuestros transportadores de rebaba superan las expectativas, incluso en los entornos de producción más exigentes, y lo hacen de manera más eficiente y con menos mantenimiento que otras soluciones de extractores.
CARACTERÍSTICAS ESTÁNDAR
• Protección contra sobrecarga/atascos
• Transmisión de velocidad variable (1,1 m/min - 3,3 m/min)
• Colores de pintura - azul / blanco / gris / negro
• Ángulo de inclinación - 60* / 45*
CARACTERÍSTICAS OPCIONALES
• Depósitos de refrigerante
• Rieles de acero inoxidable para carga pesada
• VFD o caja de control
• Filtración de refrigerante (CDF - Filtración por disco de virutas)
• Color de pintura personalizado
• Ángulo de inclinación personalizado
• Limitador de par elevado (1,6 m/min, 2,2 m/min, 3,0 m/min)
• Toberas personalizadas
CONTACTO
Información de contacto
Contáctanos para obtener más información sobre nuestros productos.
Teléfono: (Nacional) 55 5318 4146
(Extranjero) +52 55 5318 4146
Correo: ventas@grupogaden.com
Dirección: Silca N°4 Col. Vista Hermosa,Tlalnepantla, Edo. de México CP. 54080